附着力1级固含量80%,99%包装规格25千克/组平米用量0.3千克/平米执行标准GB/T5750-2006分类底漆,中涂,面漆使用方法辊涂刷涂型号8710-1 8710-2 8710-3
8710环氧饮用水涂料底漆作用:
1、封闭基础地面
环氧底漆的一个首要作用就是封闭基础的地面。具体体现在抗反碱、均衡地面吸水能力等方面,有些墙面碱性较强,经潮气、水等浸泡后产生碱花,严重时在漆膜表面形成层碱霜,终使漆膜破坏。环氧底漆可以起封闭作用,缓解这种情况。涂刷底漆是为了确保施工后整个环氧地坪漆膜色泽、光泽、光感统一且均匀,有一个很好的美观效果。
2、加固基础地面
加固基础地面也是环氧底漆的作用之一。对于有些轻微起砂起灰的基础地面,通过加大环氧底漆的用量,能有效快速的渗透进地面,提升地面的强度,很大程度的提高环氧地坪的使用寿命。
3、增强涂层附着力
增强环氧地坪漆涂层附着力,这也是环氧底漆的作用。底漆中树脂含量较高,附着力较强。可提高漆膜与地面的粘结力。避免直接涂刷面漆会出现起皮起壳、表面效果差的问题。
二、8710食品级环氧底漆的特点
1、环氧底漆具有封闭的特点。能隔绝水汽、潮气,达到防水效果,防止水汽渗透引起的返潮。所以也让底漆起到了封闭基础地面的作用。
2、环氧饮用水涂料底漆有的渗透性可以渗透到基础地面2mm,有一定的补强基础地面的强度, 针对基础地面有轻微的起砂、起粉情况,可以直接用环氧底漆来增加基面的强度。
3、附着力强。能很好地粘接附着在基面上,还能与中涂层形成良好的粘接性效果,避免与基面、中涂层脱层。
4、适应不同的基础地面。如:混凝土、水磨石、金钢砂、陶瓷、新旧基面均可使用。
环氧饮用水涂料底漆层是的,它有封闭、加固基础地面及增强涂层附着力的重要作用。而好的环氧底漆,不仅能增强基础地面的强度,提高涂层附着力,具有抗碱、防潮等功能,同时还可均衡基础地面对面漆的吸收程度,确保面漆的光泽和颜色均匀,提高面漆装饰效果。
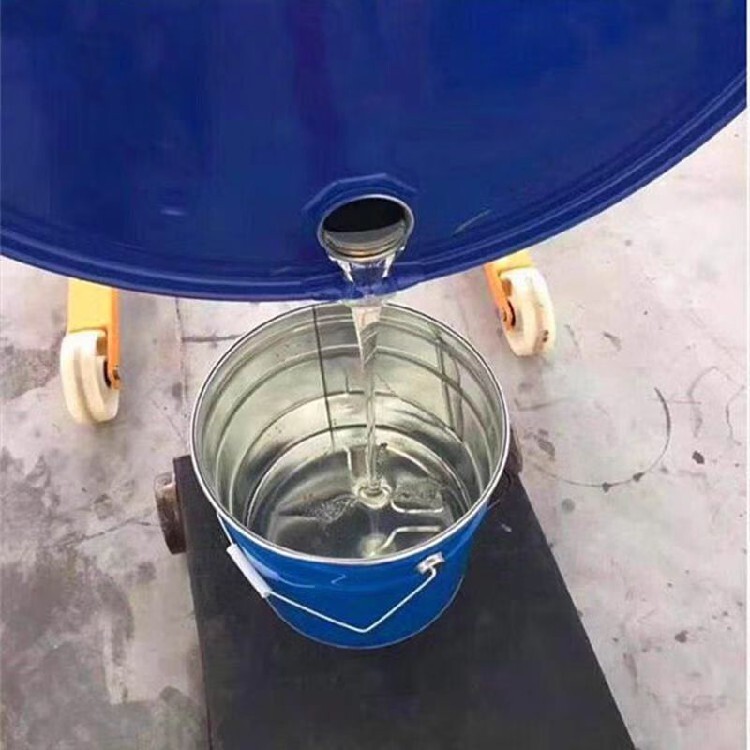
环保型无溶剂环氧涂料简介
一:对大气环境的保护低挥发性有机化合物(VOC)排放,传统溶剂型涂料在施工和干燥过程中会释放大量的 VOC,这些有机化合物不仅对大气造成污染,还会在一定程度上形成光化学烟雾,影响空气质量和人们的健康。而无溶剂环氧涂料基本不含有机溶剂,VOC 排放量极低,甚至可以达到零排放,大大减少了对大气环境的负面影响。例如,在一些城市的工业集中区和建筑工地,如果广泛使用无溶剂环氧涂料,可有效降低周边区域的空气污染指数,改善居民的生活环境。该产品完全符合国家环保政策的需求。
二:减少温室气体排放有机溶剂的生产和使用过程中会产生大量的温室气体,如二氧化碳等。无溶剂环氧涂料由于不使用有机溶剂,在生产和施工环节减少了温室气体的排放,有助于缓解全球气候变化的压力。以一个大型的工业防腐项目为例,若采用无溶剂环氧涂料代替传统溶剂型涂料,可显著降低整个项目的碳排放量,为实现国家的碳达峰、碳中和目标做出贡献。
三:对水资源的保护无溶剂泄漏风险,与溶剂型涂料相比,无溶剂环氧涂料在储存、运输和使用过程中不存在溶剂泄漏的问题。有机溶剂泄漏不仅会污染土壤,还可能渗入地下,对地下水造成污染。无溶剂环氧涂料的使用可以有效避免这种风险,保护水资源的安全。在一些对水资源保护要求较高的地区,如水源地附近的工业设施和基础设施建设中,使用无溶剂环氧涂料可以确保不会因涂料泄漏而对地下水造成污染。
四:对人体健康的保护降低职业健康风险,溶剂型涂料中的有机溶剂在施工过程中会挥发,施工人员长期接触这些有机溶剂,容易引发呼吸道疾病、神经系统损伤等健康问题。无溶剂环氧涂料无有机溶剂挥发,施工人员在施工过程中接触到的有害物质大大减少,降低了职业健康风险。对于从事涂料施工的工人来说,使用无溶剂环氧涂料可以提供一个更加安全的工作环境,减少职业病的发生几率。
五:可持续发展的推动资源节约无溶剂环氧涂料的生产过程中不需要大量的有机溶剂,节约了石油等自然资源。同时,由于其使用寿命长、性能稳定,减少了涂料的频繁更换和浪费,实现了资源的有效利用。从长远来看,推广无溶剂环氧涂料有助于推动涂料行业向资源节约型、环境友好型方向发展,实现可持续发展的目标。
六:推进产业升级随着环保要求的不断提高,无溶剂环氧涂料等环保型涂料的市场需求逐渐增大。这将促使涂料企业加大研发投入,提高技术水平,推动涂料产业的升级换代。
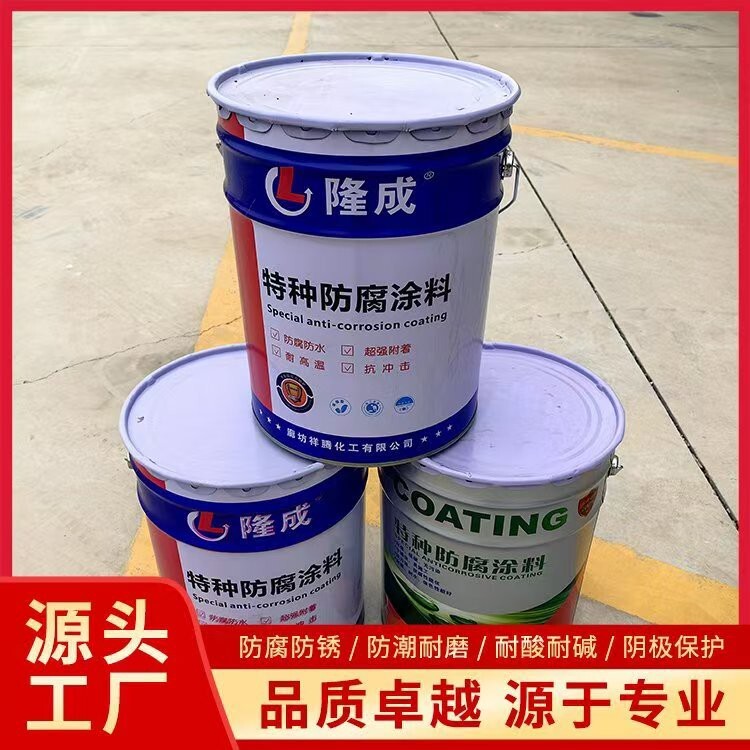
无溶剂环氧树脂底漆制作工艺主要包括:选择合适的原材料、确定配比和混合工艺、以及固化过程的控制等。这种底漆以其环保、耐腐蚀等特点,在工业涂装领域得到了广泛应用。以下是具体探讨:
1. 选择原材料
环氧树脂的选择:选择低分子量的液态环氧树脂,如E-44,有助于降低涂料的黏度,提高施工效率。
活性稀释剂的应用:使用甲苯基缩水醚、苯基缩水甘油醚、丁基缩水甘油醚等活性稀释剂调整黏度,其用量一般小于树脂质量的15%。
固化剂的选择:常用的固化剂包括多元胺和低分子量聚酰胺,根据实际需要选择合适的固化剂类型以适应不同的固化环境和要求。
2. 确定配比和混合工艺
组分比例的确定:按照一定的比例将环氧树脂与固化剂混合,确保两者充分反应,实现理想的涂层性能。
混合均匀性的要求:在混合过程中要确保两组分充分融合,避免局部配比不均影响涂层性能。
3. 固化过程的控制
常温固化与加速剂的使用:在常温下可进行固化,但为了提高固化速度,可适当加入加速剂,如苯酚、水杨酸等。
促进剂的应用:在低温条件下,加入适量的促进剂DMP-30可以提高固化效率,用量为聚酰胺的1%。
4. 施工方法的选择
设备施工:采用热喷涂或双口喷枪喷涂,确保涂料均匀涂布于基材表面。
配合比例与熟化:涂装前需按比例配合两组分,必要时进行熟化处理后施工。
5. 干燥与固化
常温干燥:一般情况下,采用常温干燥即可实现涂层的固化。
-烘干固化:对于绝缘材料的涂覆,可能需要通过烘干的方式来加速固化过程。
此外,在了解上述内容后,还需注意以下几点:
环保性:由于无溶剂环氧涂料几乎不含有机溶剂,VOC含量极低,因此更加绿色环保。
一次成膜厚度:无溶剂环氧涂料的一次成膜厚度可达200-300μm,提供了良好的防腐能力。
应用范围:适用于通风不良环境的设备涂装,如海上采油设备、装载石油的船舱、槽车、环氧地坪漆施工,是一种重要的重防腐涂料。
总的来说,无溶剂环氧树脂底漆制作工艺涉及了对原材料的精心选择、的配比和混合、固化过程的严格控制以及适宜的施工方法。这些特点使得无溶剂环氧树脂底漆在实际应用中展现出的性能,满足了现代工业对、环保涂料的需求。