施工时间24h附着力1级包装规格25千克漆膜厚度120um表干时间2h可定制颜色灰色,蓝色,黄色,绿色等平米用量0.3千克涂装间隔6h固含量80%
佐涂环氧饮用水标准防腐涂料8710-3涂料使用方法
1):该漆使用前充分搅拌均匀,把被涂物处理干净,严防油污、水份、灰尘及其他污物存在(建议喷沙除锈
至Sa2.5级或手工除锈至St3级),以涂刷质量。施工开桶时。
2):涂料配比为:
各 色 漆:甲组分(基料)25公斤:乙组分(固化剂) 5公斤。(或按厂家提供的数量配比)
银色面漆:甲组分(基料)15公斤:乙组分(固化剂) 3公斤。(或按厂家提供的数量配比)
3):施工配比方法为:将甲组分大口打开,将乙组分加入甲组分内,充分搅拌均匀。熟化(静止)30分钟,即可进行涂装。
4):涂装环境温度一般为5度--40度,空气相对湿度不超过85%,工件表面温度至少应露点温度3度以上,寒冷和潮湿的环境会使涂层干燥速度减慢。
4):此材料要求随配随用,配比后的涂料须在六小时之内用完。未配完的材料要密封保存。
5):阴雨天或相对湿度大于75%时应停止施工。 对于腐蚀介质严重的部位,建议多道涂刷。
6):产品应存放在阴凉干燥处,防止日光直接照射,隔绝火源,远离热源。贮存期为十二个月。
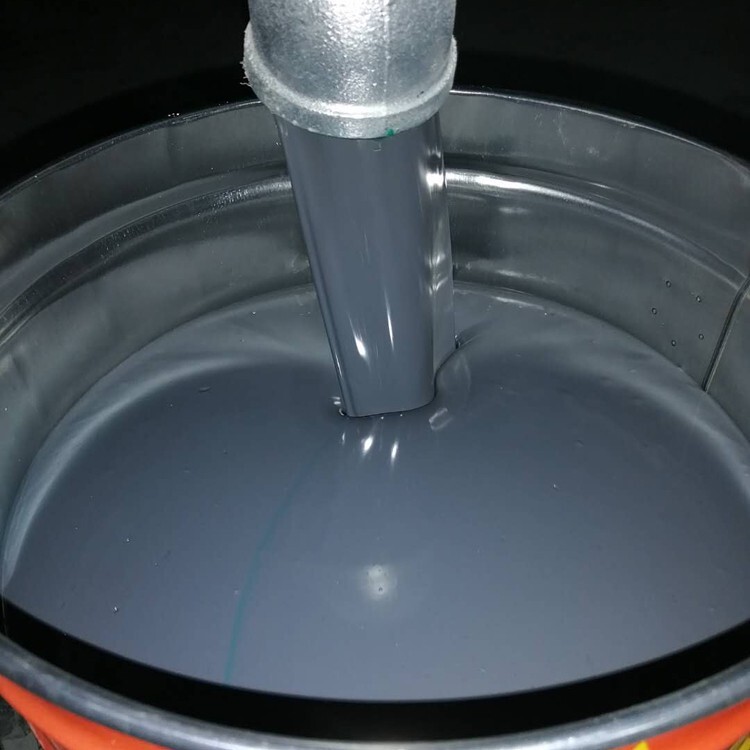
施工步骤:使用(施工)说明
步骤一: 观察基材是否有水,油,锈,新做水泥地板需要养护30天以上才可施工。
步骤二:观察基材是否有不平整的地方:如:装修残留水泥渣水泥块,影响附着力的杂物需清理干净。
步骤三:查看油漆包装桶上的合格证标签,注意查看比例和需要涂刷的颜色,调配好的油漆需在5小时内用完,否则会变成粘稠状不好涂刷。
步骤四:先用羊毛刷把墙角边进行涂刷。
步骤五:用滚筒进行十字交叉方式进行滚刷。
步骤六:刷好的油漆应进行养护24小时以上才可以走人。
步骤七:完全干燥需七天,完工地坪养护七天后即可使用。
保质期:在正常储运条件下,自制造之日起12个月。
声明: 鉴于产品的涂装和使用条件不在本公司的控制范围内,本公司仅对所提供的产品的质量本身负责。
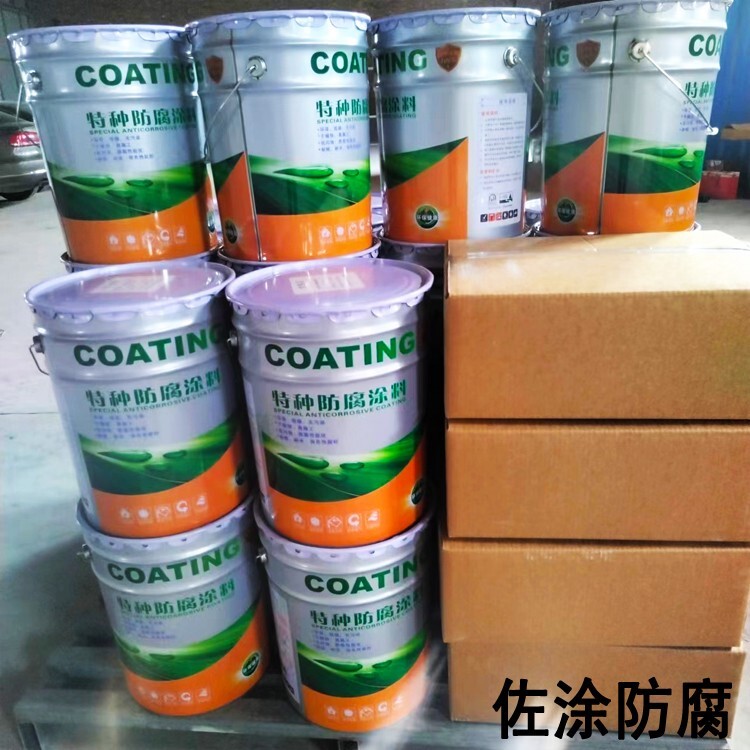
水性环氧树脂是环氧树脂以微粒或者是液滴的形式分散在以水为连续相的介质中而配制成的稳定的树脂材料。水性环氧树脂除了具有溶剂型环氧树脂涂料的优点外,的优势表现在室温和潮湿环境下固化,可以与金属粘结及非金属混合,如水泥、石灰、石膏等水性胶结物配合,提高早期强度,提高韧性,增强防水性能。这是其他水性树脂如水性丙烯酸材料和水性聚氨酯材料所无法比拟的。
水性环氧涂料是具有水性环氧树脂改性聚酰胺树脂及其他辅助材料配制而成的,一般为双组分构成(疏水性的环氧树脂分散体乳液,亲水性的胺类固化剂)。水性环氧树脂乳液是在一定高温高速剪切作用下将乳化剂和环氧树脂混合均匀,使得整个体系由“油包水”向“水包油”转变,形成均匀稳定的水可以稀释的环氧树脂。实际应用时,加入适量的固化剂,环氧树脂还原固化,水被置换出来。
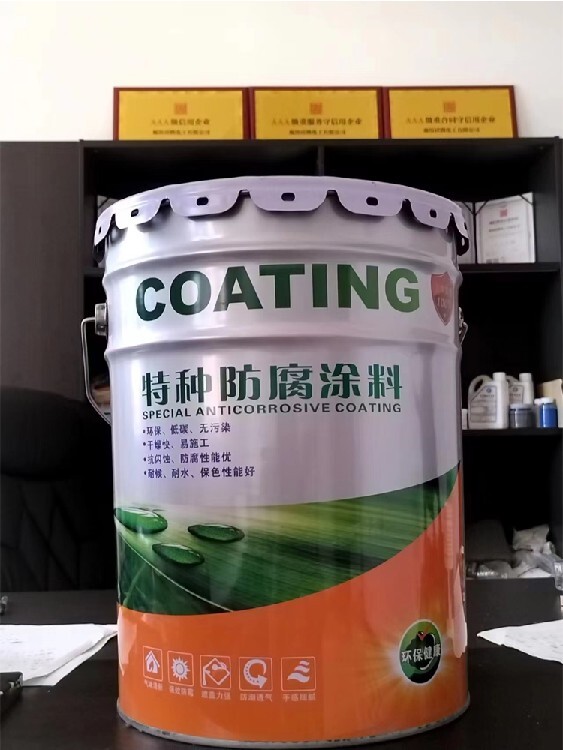
水性环氧树脂及其涂料具有诸多的优良特性,笔者简单的罗列了实际应用中所表现出来的特点,性能如下:
1. 优良的附着力,可以和各种金属、非金属直接粘结,号称“胶”。
2. 良好的耐化学腐蚀性能,成膜后的水性环氧树脂及其涂料含有稳定的苯环及醚键,分子结构紧密,因此对化学介质具有较好的稳定性。
3. 品种的多样性与广泛的适应性,环氧树脂及其固化剂品种繁多,可以通过改变配方以适应不同的施工条件和应用环境。
4. 不燃烧,气味小,水性环氧树脂及其涂料无溶剂,水为稀释剂,因此不会燃烧,而且没有什么味道,对于运输和密闭空间施工的安全,有着重大的经济意义和社会意义。
5. 可以在无明水潮湿基面上施工并且固化。
6. 施工工具和被污染了的物件容易用水清洗,卫生,简单,方便。
7. 耐冲击,耐磨,固化养护后的涂层可以承受250KPa的水压。
8. 水性环氧树脂及其涂料可以用装饰性面漆或者工业面漆覆涂。
9. 可以安全使用于健康敏感区域,如食品区,饮用水区,居住区等,对环境没有污染。
10. 取代混凝土洒水或者薄膜养护,初凝混凝土涂覆水性环氧树脂及其涂料形成养护膜,可以防止水分蒸发过快,有助于混凝土的养护和封闭。
11. 环氧树脂固化收缩率小,一般为 1%-2%,是热固性树脂中固化收缩率小的品种之一(酚醛树脂为 8%-10%;不饱和聚酯树脂为 4%-6%;有机硅树脂为 4%-8%)。线胀系数也很小,一般为 6×10-5/℃。所以其产品尺寸稳定,内应力小,不易开裂。
12. 环氧树脂电性能好,是热固性树脂中介电性能好的品种之一。
13. 环氧固化物的耐热性一般为80-100℃。环氧树脂的耐热品种可达200℃或更高。
14. 水性环氧树脂及其涂料可以作为其他涂层施工前不吸水或易于受污染的底涂料。
15. 水性环氧树脂及其涂料可以作为水泥添加剂,以形成强度不同的修复砂浆及防水填缝材料。
16. 高强度裂缝修复混合物,用于混凝土的结构修复。
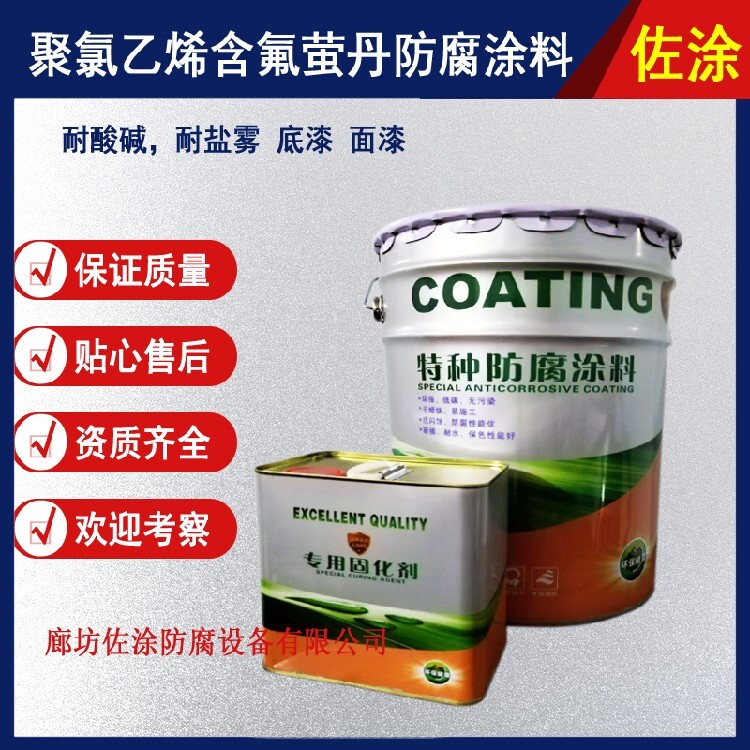
环氧树脂、酚醛树脂干混复配后能够提高整体防腐效果,延长设施使用寿命并且大大降低运行维护成本。原先单一的环氧树脂和单一的酚醛树脂在重防腐防护环境中不再是“单打斗”“孤军奋战”;而是“携手联盟”“团结协调”,共同实现的防护屏障。防腐施工中环氧树脂多采用6101#(E-44),具有非常的粘结性,号称“胶”,良好的耐碱性,的耐水性,能够在一定的温度下(≤100℃)使用,固化时没有小分子挥发物质产生;但是其大的缺点就是不耐氧化剂,也不耐紫外线,耐酸性差,如硝酸,浓硫酸等。酚醛树脂现在常用的就是2130#,它对非氧化性酸如盐酸、稀硫酸、磷酸以及盐类、溶剂、水等有良好的耐腐蚀性能、能够在120℃-150℃环境下使用;但是其耐碱性能比较差,粘结性不如环氧树脂。防腐蚀技术人员根据环氧树脂和酚醛树脂的不同理化性能,针对具体的腐蚀环境和工艺要求,将这两种树脂按照不同的重量比例混合在一起,互相取长补短,取得单一树脂所不能达到的综合性能。
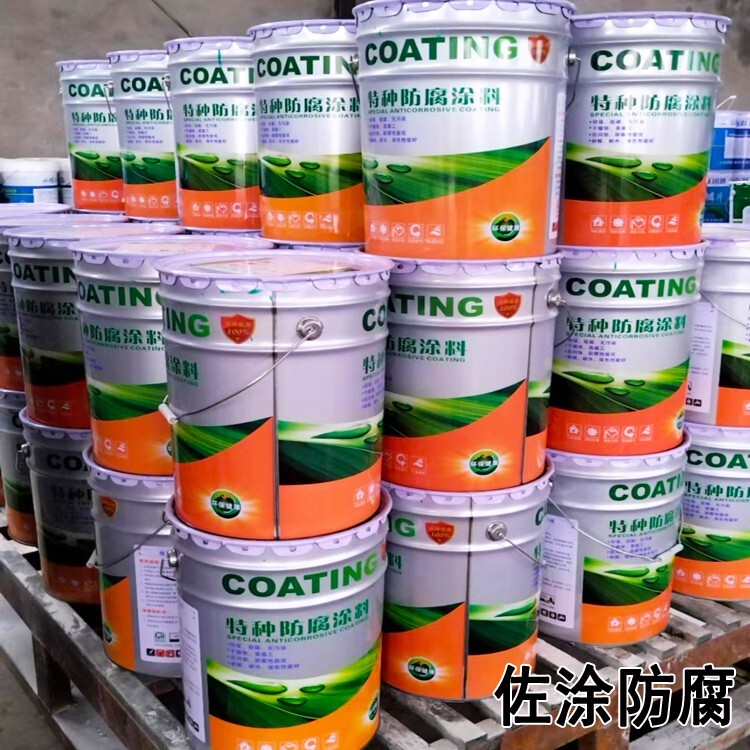
环氧树脂和酚醛树脂干混复配后的树脂可以配制成涂料、鳞片胶泥、玻璃钢等防腐材料。常用干混复配比例有7:3和6:4两种重量比,即环氧树脂:酚醛树脂=70:30和60:40,占比不同性能也有差别,如7:3稍偏向环氧树脂性能;而6:4稍偏向酚醛树脂性能。干混复配后的环氧、酚醛混合型树脂固化依然采用环氧树脂的固化剂(如乙二胺,T31,腰果固化剂等),加入量乙二胺为6-8份,T31为10-15份;但是环氧固化剂实际加入量还需要随着环境温度的变化进行变动和调整,笔者强烈建议经过现场小样试验确定固化剂配比量,冬季施工提倡使用冬用型树脂。环氧、酚醛干混时按照各自重量比例预先“开稀”,“开稀”时不宜过多加入稀释剂,否则会影响漆膜层厚度或者树脂固含量过低造成粘结性能下降及其他性能的改变。然后将“开稀”后的酚醛树脂边搅拌边缓缓加入“开稀”后的环氧树脂中,使用电动搅拌器进行分散搅拌,当混合树脂颜色统一均匀,无有分层时可以停止搅拌,静置备用。干混时严禁水或者其他杂物进入,严禁再次添加稀释剂,复合树脂的纯度和粘度,使用时直接加入环氧固化剂搅拌均匀,静置5分钟即可。复配时准确掌握好重量比,否则因为计量不准将直接影响防腐效果。干混后的复配树脂建议一次性用完,边配边用,以免早期固化,造成材料浪费。干混复合后的环氧、酚醛混合型树脂兼具耐酸、耐碱、耐溶剂、耐热、粘结性和机械性。这些的特性赋予环氧、酚醛混合型树脂更宽泛的应用领域,如污水池、室内钢结构、车间彩钢瓦、钢平台、烟筒、管道,特别是大量应用于酸性或者高温环境下的储罐、容器衬里等。